Францускиот институт за соларна енергија ИНЕС разви нови PV модули со термопластика и природни влакна добиени во Европа, како што се лен и базалт. Научниците имаат за цел да го намалат стапалото на животната средина и тежината на соларни панели, истовремено подобрувајќи го рециклирањето.
Рециклирана стаклена панел на предната страна и ленен композит на задниот дел
Слика: ГД
Од списанието ПВ Франција
Истражувачите од Националниот институт за соларна енергија на Франција (ИНЕС)-поделба на француската Комисија за алтернативни енергии и атомска енергија (ЦЕА)-развиваат соларни модули со нови био-базирани материјали од предната и задната страна.
„Бидејќи јаглеродниот отпечаток и анализата на животниот циклус сега станаа суштински критериуми во изборот на фотоволтаични панели, изворите на материјали ќе станат клучен елемент во Европа во следните неколку години“, рече Анис Фуини, директорот на ЦЕА-ИНЕС , во интервју за списанието ПВ Франција.
Ауд Дериер, координатор на истражувачкиот проект, рече дека нејзините колеги ги разгледале различните материјали што веќе постојат, за да најдат оној што може да им овозможи на производителите на модули да произведуваат панели што ги подобруваат перформансите, издржливоста и трошоците, додека го намалуваат влијанието врз животната средина. Првиот демонстратор се состои од соларни ќелии на хетерохункција (HTJ) интегрирани во ол-композитен материјал.
„Предната страна е изработена од полимер исполнет со фиберглас, кој обезбедува транспарентност“, рече Дериер. „Задната страна е изработена од композит заснован на термопластика во која е интегрирано ткаење на две влакна, лен и базалт, што ќе обезбеди механичка сила, но и подобар отпор на влажност“.
Ленениот леб е изворен од северна Франција, каде веќе е присутен целиот индустриски екосистем. Базалтот е изворен на друго место во Европа и е ткаен од индустриски партнер на ИНЕС. Ова го намали отпадот од јаглерод за 75 грама CO2 на вати, во споредба со референтен модул со иста моќност. Тежината беше исто така оптимизирана и е помалку од 5 килограми на метар квадратен.
„Овој модул е насочен кон PV на покривот и градење интеграција“, рече Дериер. „Предноста е во тоа што е природно црна боја, без потреба од задниот сад. Во однос на рециклирање, благодарение на термопластиката, која може да се пресмета, раздвојувањето на слоевите е исто така технички поедноставно “.
Модулот може да се направи без да се прилагодат тековните процеси. Дериер рече дека идејата е да се пренесе технологијата на производителите, без дополнителни инвестиции.
„Единствениот императив е да се има замрзнувачи за складирање на материјалот и да не се започне со процесот на вкрстено поврзување на смолата, но повеќето производители денес го користат Prepreg и веќе се опремени за ова“, рече таа.
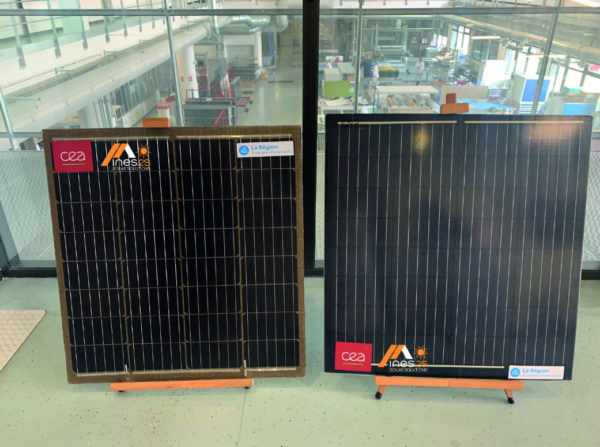
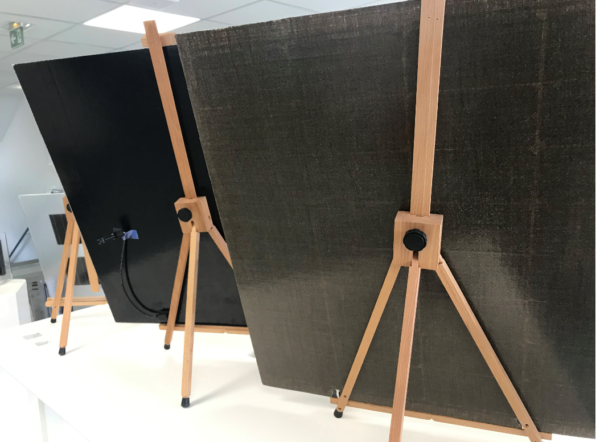
„Работевме на вториот живот на стакло и развивме модул составен од повторно користено стакло од 2,8 мм што доаѓа од стар модул“, рече Дериер. „Ние, исто така, користевме термопластичен енкапсулант кој не бара вкрстено поврзување, што затоа ќе биде лесно за рециклирање, и термопластичен композит со ленено влакно за отпорност.“
Задното лице без базалт на модулот има природна боја на постелнина, што може да биде естетски интересно за архитектите во однос на интеграцијата на фасадата, на пример. Покрај тоа, алатката за пресметување INES покажа намалување од 10% во отпадот од јаглерод.
„Сега е императив да се доведат во прашање фотоволтаичните синџири на снабдување“, рече ouуини. „Со помош на регионот Рона-Алпес во рамките на меѓународниот план за развој, затоа отидовме во потрага по играчи надвор од сончевиот сектор за да најдеме нова термопластика и нови влакна. Размислувавме и за тековниот процес на ламиниране, кој е многу енергетски интензивен “.
Помеѓу притисокот, притискањето и фазата на ладење, ламинацијата обично трае помеѓу 30 и 35 минути, со работна температура од околу 150 C до 160 C.
„Но, за модулите кои сè повеќе вклучуваат еко-дизајнирани материјали, неопходно е да се трансформира термопластика на околу 200 Ц до 250 Ц, знаејќи дека HTJ технологијата е чувствителна на топлина и не смее да надминува 200 Ц“, рече Дериер.
Институтот за истражување се здружува со специјалист за термокомпресија со седиште во Франција, Рокул, за да ги намали времињата на циклусот и да направи форми според потребите на клиентите. Заедно, тие развија модул со задно лице изработено од термопластичен композит од полипропилен-тип, на кој се интегрирани рециклирани јаглеродни влакна. Предната страна е изработена од термопластика и стаклена стакло.
„Индукцискиот процес на термокомпресија на Рокул овозможува брзо загревање на двете предни и задни плочи, без да се достигнат 200 C во јадрото на клетките на HTJ“, рече Дериер.
Компанијата тврди дека инвестицијата е помала и процесот може да постигне време на циклус од само неколку минути, додека користи помалку енергија. Технологијата е насочена кон композитни производители, да им се даде можност за производство на делови од различни форми и големини, додека се интегрираат полесни и потрајни материјали.
Време на објавување: јуни-24-2022